Stitch & Glue Shed
This project repurposes stitch and glue kayak building technology into a new shed prototype for Mahama refugee camp, Rwanda. The manufacture process consists of utilizing flat pieces, specifically plywood. Five pieces of veneer are oriented in different directions to create one piece of plywood – they are monoclastic, meaning that they can only bend in one direction. When the flat pieces are stitched together, each flat piece curves to meet the adjacent piece. This creates a low tech double curvature between the panels. This complex geometry that is formed is what gives an enormous amount of rigidity and makes the structure.
Manufactured out of ½ inch flat plywood pieces, the shelter technology allows it to be a very thin yet rigid shell. Therefore, it is easy to be packed and shipped to our predetermined site at the Mahama refugee camp. For insulation, local construction workers will mix pulverized styrofoam with water to create a lightweight cementitious matrix, which they will hand trowel onto the structure on site. For waterproof, workers will apply another layer of natural, readily available, and replenishable oil wax, such as beeswax to seal the shell.
An inner shell and an outer shell create a plenum space that allows cross ventilation. The windows allow for ventilation from side to side. Ventilation buttons at the top block rain while allow air travel. Perpendicular braces hold the shells in place and allow air travel. The base is a pedestal that raises the shell up to avoid moisture / flooding / mudslides. It is made out of fiber reinforced concrete nailed down to the base. The trusses are connected to the fiber reinforced concrete which hold the plywood floor plate.
Fall 2020, collab with Andrea Gomez.
This project repurposes stitch and glue kayak building technology into a new shed prototype for Mahama refugee camp, Rwanda. The manufacture process consists of utilizing flat pieces, specifically plywood. Five pieces of veneer are oriented in different directions to create one piece of plywood – they are monoclastic, meaning that they can only bend in one direction. When the flat pieces are stitched together, each flat piece curves to meet the adjacent piece. This creates a low tech double curvature between the panels. This complex geometry that is formed is what gives an enormous amount of rigidity and makes the structure.
Manufactured out of ½ inch flat plywood pieces, the shelter technology allows it to be a very thin yet rigid shell. Therefore, it is easy to be packed and shipped to our predetermined site at the Mahama refugee camp. For insulation, local construction workers will mix pulverized styrofoam with water to create a lightweight cementitious matrix, which they will hand trowel onto the structure on site. For waterproof, workers will apply another layer of natural, readily available, and replenishable oil wax, such as beeswax to seal the shell.
An inner shell and an outer shell create a plenum space that allows cross ventilation. The windows allow for ventilation from side to side. Ventilation buttons at the top block rain while allow air travel. Perpendicular braces hold the shells in place and allow air travel. The base is a pedestal that raises the shell up to avoid moisture / flooding / mudslides. It is made out of fiber reinforced concrete nailed down to the base. The trusses are connected to the fiber reinforced concrete which hold the plywood floor plate.
Fall 2020, collab with Andrea Gomez.
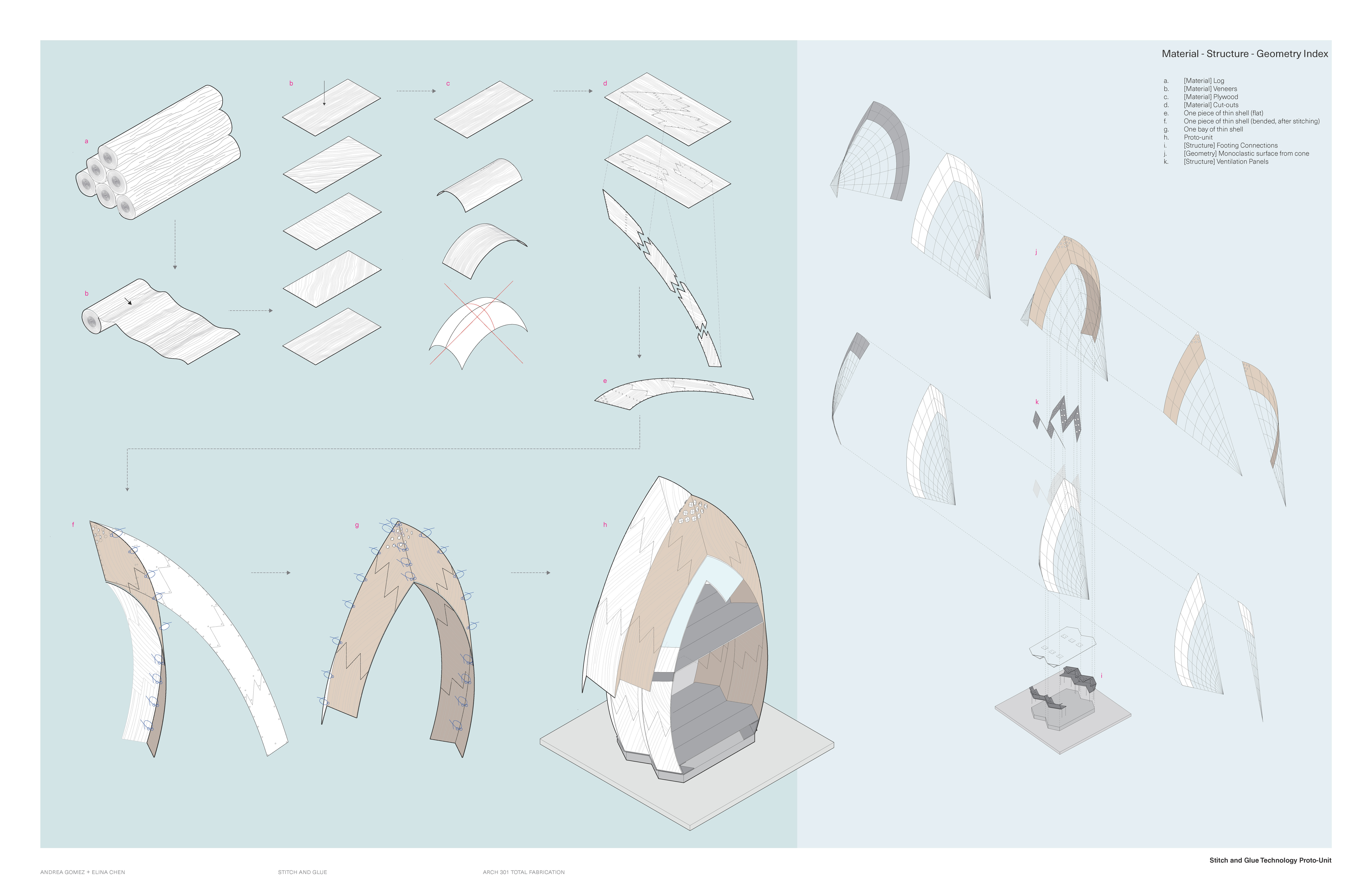

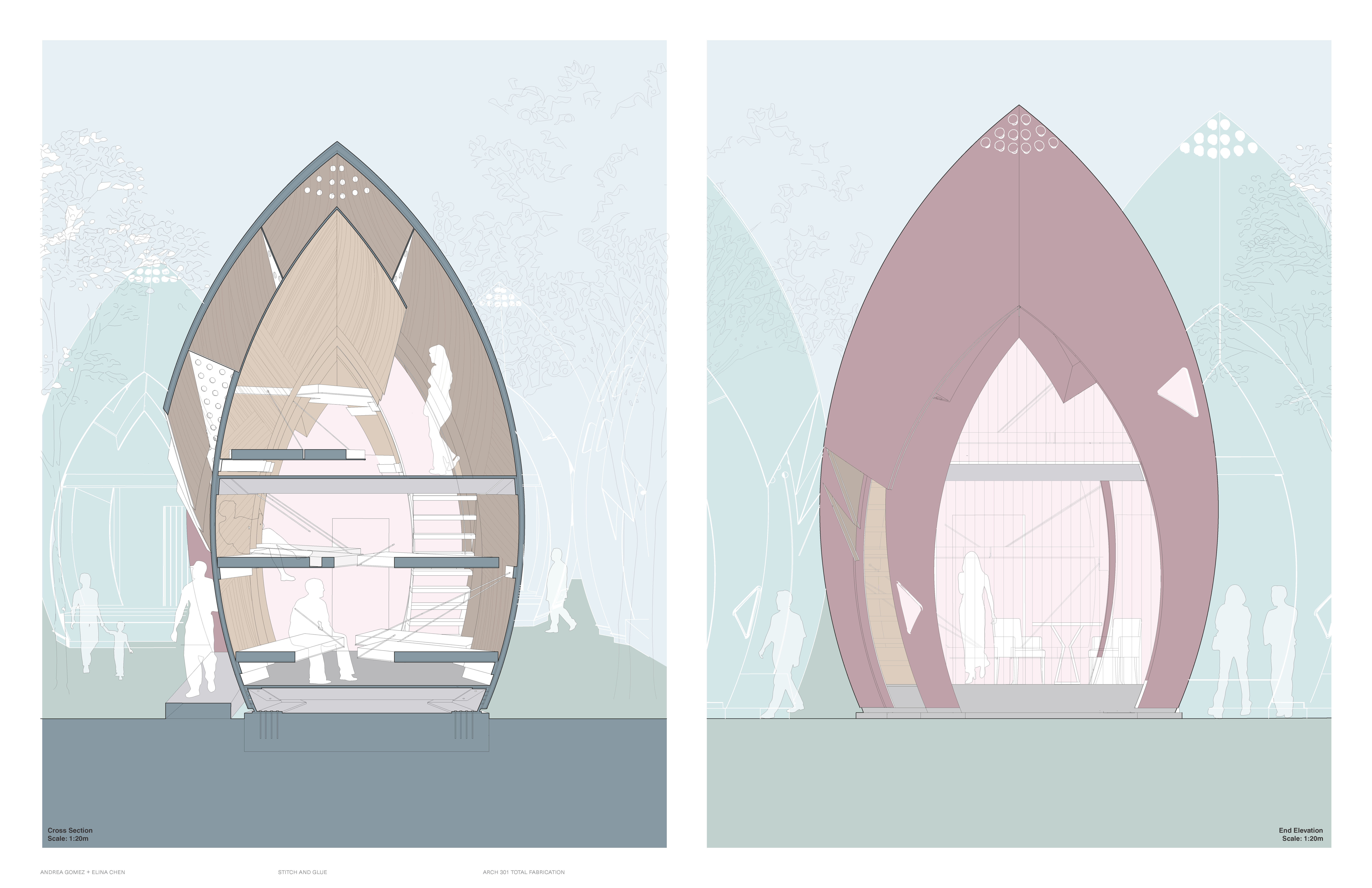
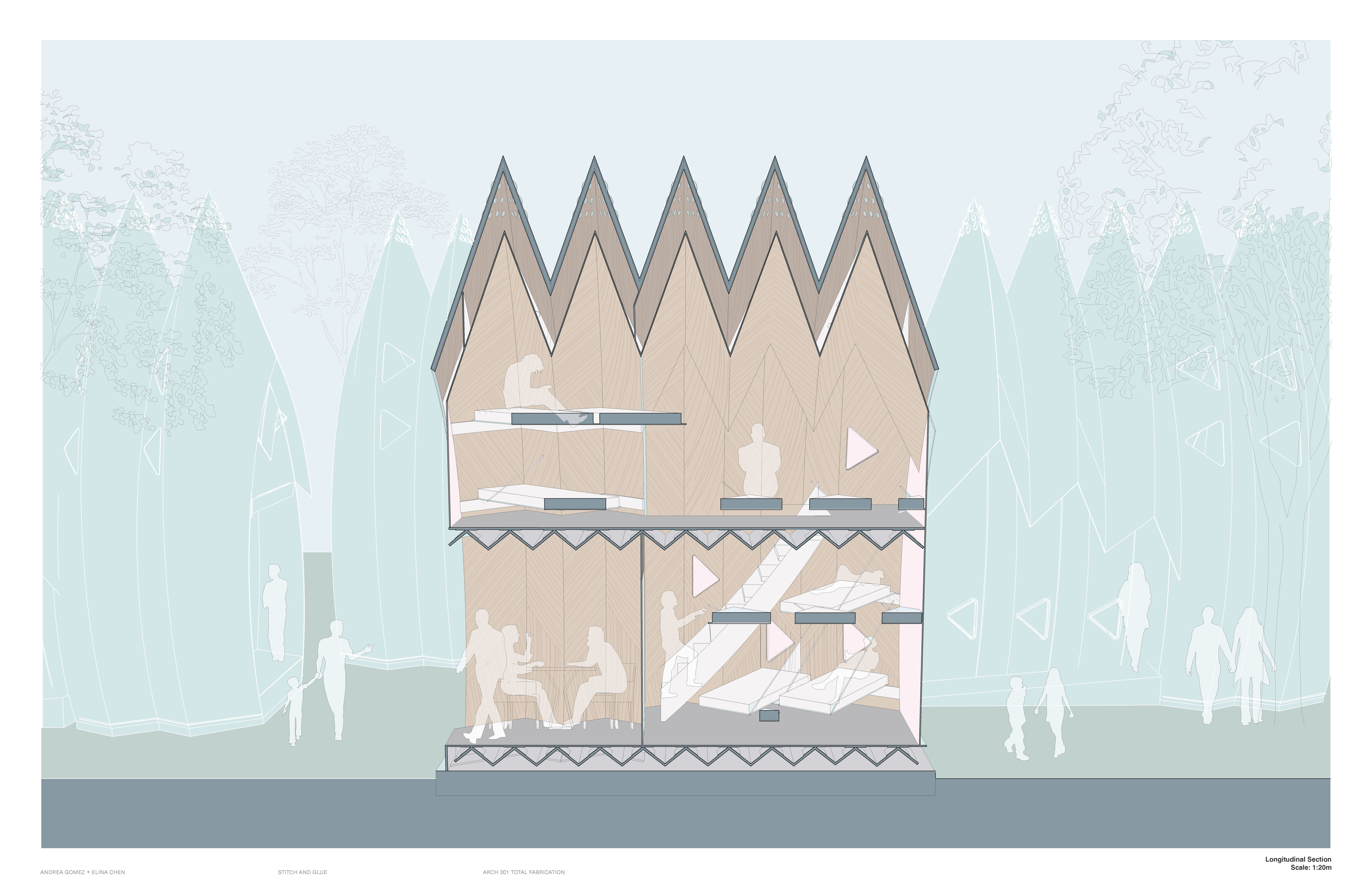
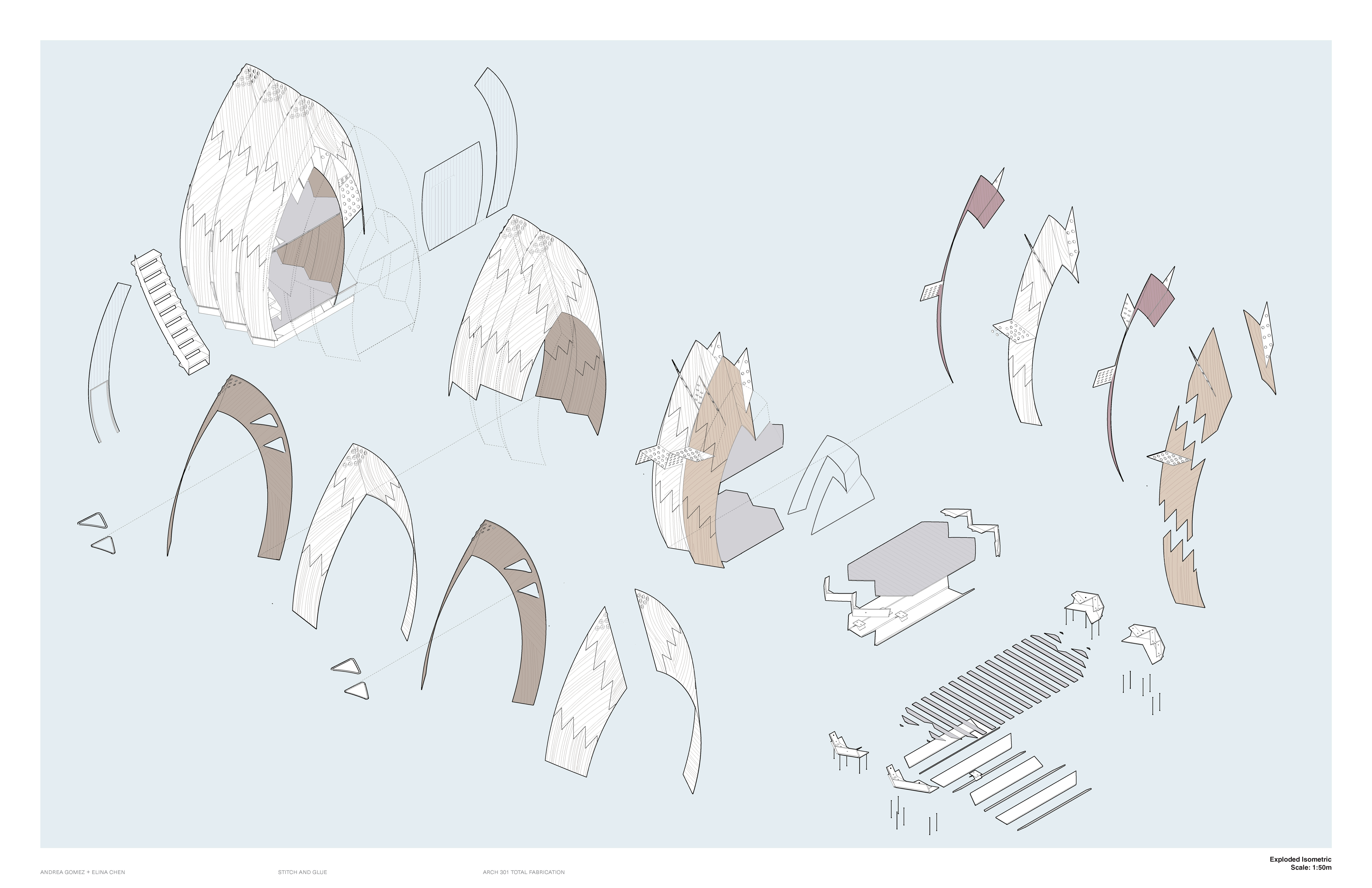
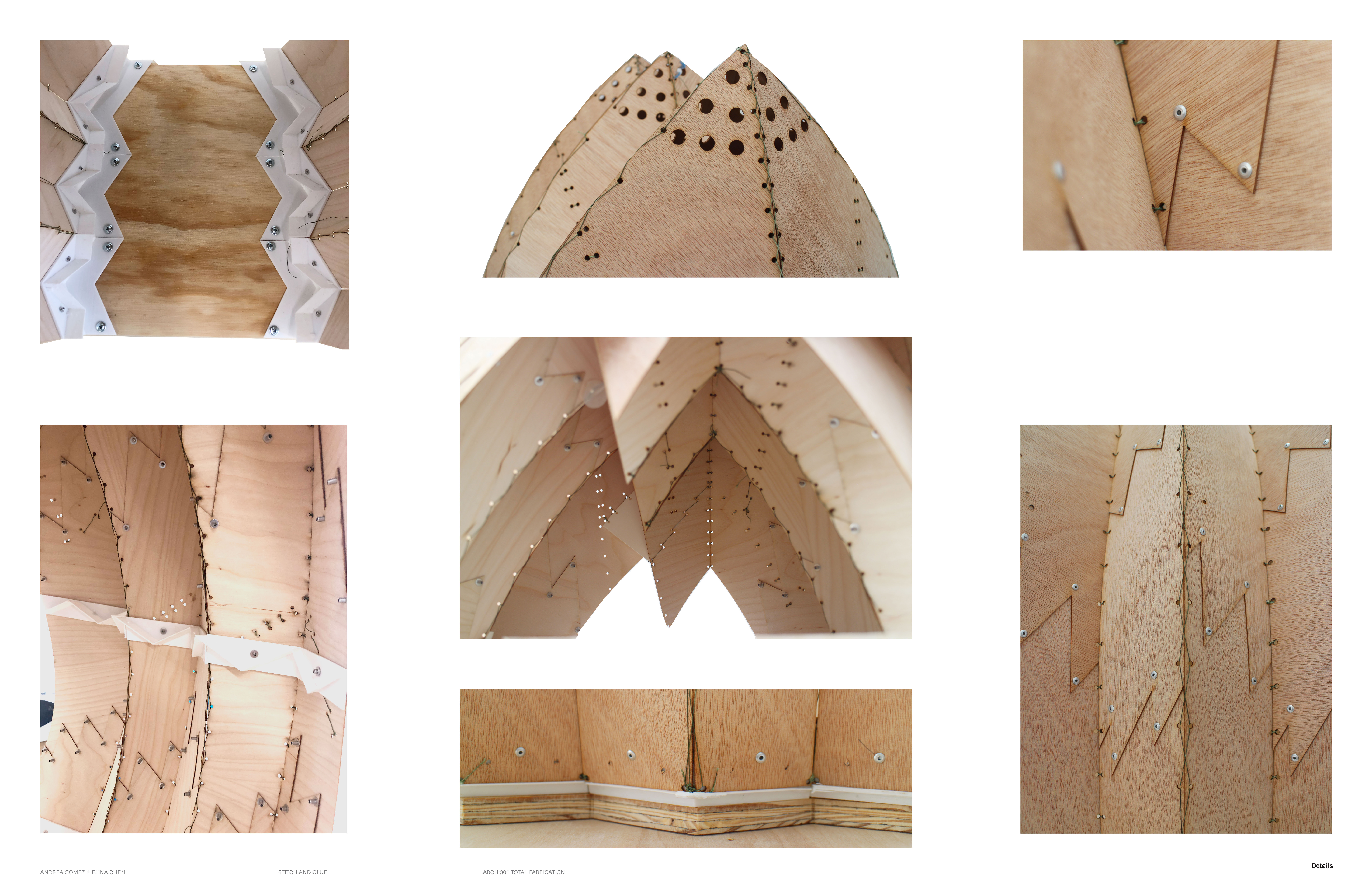
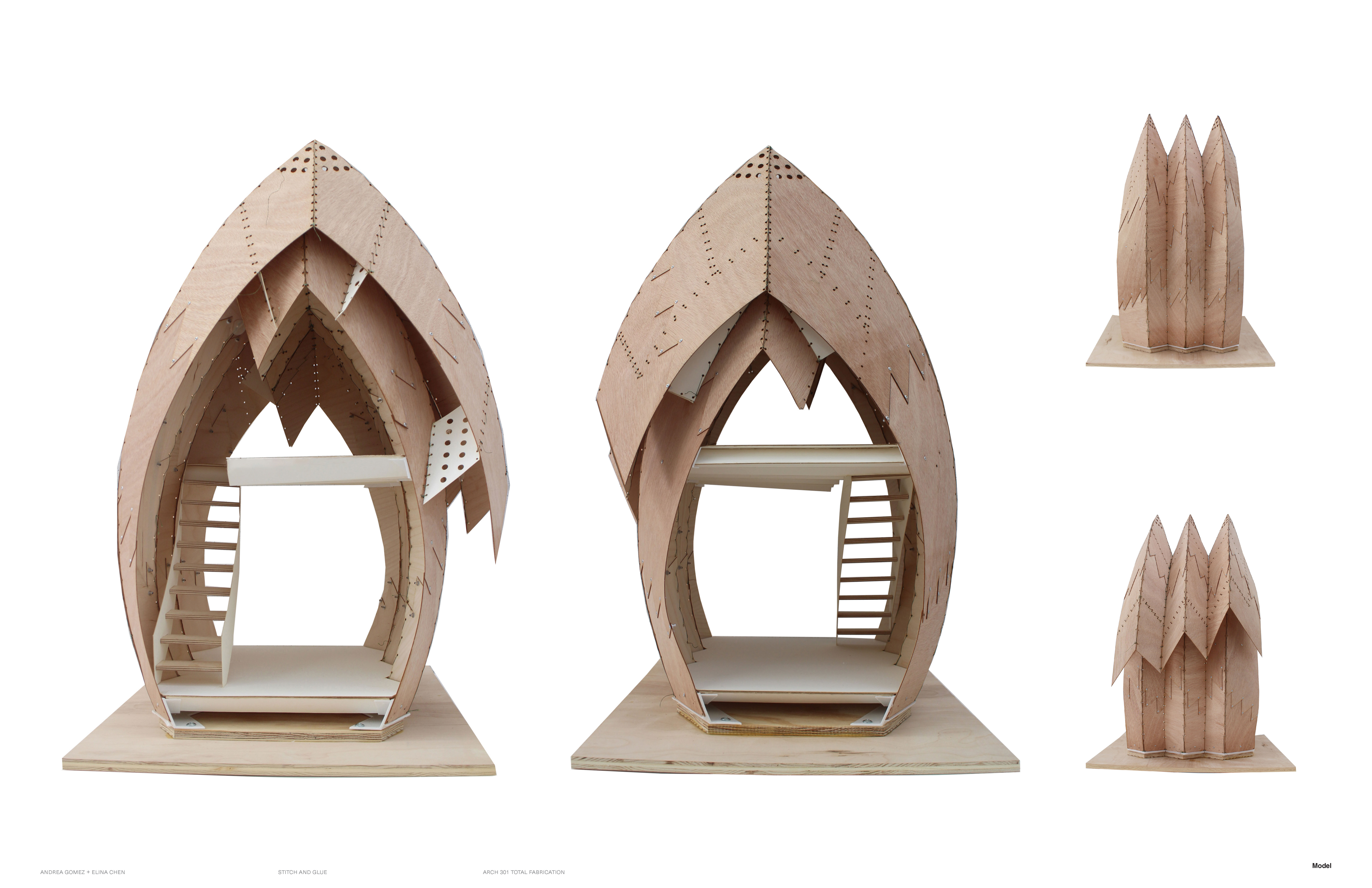